|
 |

News
|
Living With
Your Plane: The joy of living with your plane
Bill
Tuccio
8/6/2003
In January of this year I received
the approval I needed to start building my own hangar: My wife
Barbara said yes!
As I write this, I have just moved my
1994 Maule MX-7-180A into my new hangar. And while the
construction process had its challenges, they all paled in
comparison to the initial approval from Barbara.
Once
that was granted, we were fortunate enough to find a wooded
lot on a private airport community in Holt, Fla., called
Yellow River. After obtaining a copy of the covenants and
restrictions for the community and talking to other owners, it
was clear this community allowed hangars without homes. All
communities are different. It is important to find out what
your prospective aviation community allows in their documents
and what happens in practice.
By the time we closed, I
had already met with a local contractor who would clear the
land. My wife and I had marked as many trees as possible to
keep on the property while allowing for the placement of the
hangar. In a couple of hours on a Saturday morning, his
bulldozer cleared our 2/3 of an acre of trees.
Another
thing I did before the closing was to start comparing quotes
on buildings. I compared a variety of designs from
traditional, large span steel buildings to arch style
buildings to geodesic domes. The environment of the panhandle
of Florida played a large part in the questions I asked. This
environment requires a building that can meet Florida
hurricane building codes, avoid termite problems, and provide
some heat relief. After acquiring quotes from approximately
six different manufacturers and then adjusting those quotes to
compare apples to apples, I was able to select Ludwig
Buildings in Louisiana.
Equally important in the
purchase was the door selection. I was initially surprised to
find the door cost nearly half as much as the building.
Consider if you need a door at all. I spoke to some
well-reputed people who said the primary need for a door is
security, not the weather. Unfortunately, I had not considered
this advice until after my order had already been placed with
Hydroswing.
I did follow my purchase decision through
by making sure the door manufacturer and the building
manufacturer worked out all compatibility details. While both
manufacturers were very professional and did not need my
input, it gave me peace of mind to get verifications from both
parties that things were going to work out.
As Ludwig
and Hydroswing did their offsite construction, they sent
documents along the way that would be necessary to continue
construction. The first key document was the anchor bolt plan,
which allowed a local engineer to design the foundation. The
next key set of documents were the Florida engineer-stamped
plans for the door and building. With the foundation, building
and door plans in hand, I went off to the building inspector
for my approval.
I came across a little resistance
since politicians generally don't write a paragraph into the
law books for "residential hangars." The building inspectors
had to find an appropriate category and in my case it
qualified essentially as a shed. While demeaning to my
lifelong dream of having my own hangar, I didn't argue. The
permit allowed us to get electric run to the property and
break ground for the foundation.
I had looked around a
bit for someone to do the foundation and obtained some
references. I met a local contractor, David, who did land
clearing, foundation work, and marine construction. I hired
him to take on the whole project, including the foundation and
hangar erection.
David formed out the foundation and
installed the anchor bolts according to the plan. I had been
advised by numerous people to double-check the measurements of
the anchor bolts. I checked eight of the 10 anchor bolts on
the job. Unfortunately, it was the two I did not measure that
were off by about six inches. David was able to correct the
anchor bolts during the pour when he caught the error, but had
I executed my responsibility properly, things would have gone
smoother.
I was fortunate that the delivery of the
building and door occurred on the same day. This made for an
efficient use of the heavy equipment needed to get the steel
off the trucks. Both manufacturers delivered every item in
perfect condition.
I spent the weekend inventorying
every one of the more than 200 items on the shipping list for
the building, which was time well spent. Had any items been
missing, resolving the discrepancies before erection would
save valuable time.
The heavy steel of the building was
put up using a bucket loader and chains. As one can imagine,
the large steel trusses of the building are the heaviest part
of the construction and a bucket loader, fork lift or crane is
a must. The supporting steel girts (wall beams) and purlins
(roof beams) were light enough that they could be lifted into
place. Once all the steel was put in place with the hundreds
of nuts and bolts, the 2,000-pound door was lifted and welded
into place.
The steel construction took about a month,
due to a combination of weather and David's workload. With
ideal conditions and a couple extra hands, the steel can be
put up in a couple days. When the weather was not cooperating,
David was able to finish grading the property and moved about
500 yards of dirt to form a gradual slope and pad in front of
the building.
With the steel frame completed, it was
time to begin the sheeting. Early on I had been advised to
insulate the building. Being from Connecticut, I didn't really
understand why a building in Florida needed insulation, but I
came to understand that the combination of heat and noise was
greatly reduced by insulation. The insulation required that it
be in place before each piece of sheeting was applied, which
adds some time to the sheeting process. Each piece of sheeting
for the roof was about 25 feet in length, and about 12 feet
for the walls. Handling these large sheets requires some low
wind conditions and care to avoid injury.
About three
months after clearing the lot, the final trim pieces and
gutters were in place and I passed the final inspection. That
night I proudly moved my plane out of the elements and into
the hangar.
After breathing a sigh of relief, I looked
around and realized I had so many more things to do. I still
need to thoroughly clean the yard, plant grass, and adjust the
approach to the hangar. I'm going to try to slow down and
enjoy these steps. After all, that is part of what "living
with your plane" is all about.
mailto:comments@generalaviationnews.com
| |
 | |
.gif)
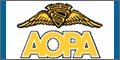
.gif)
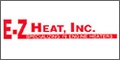
.gif)
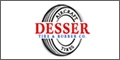
.gif)
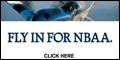
.gif)
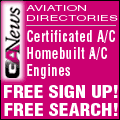
|